BLA BLA BLA VYNIL IS BETTER THAN CD, OR CD IS BETTER, WE WONT GET ANYWHERE BUT ACTUALLY WHAT IS PUT ON VYNIL NOW, IT'S SOURCE CAME FROM A PC! READ DOWN 4 MORE, SO BASICALLY THEY MUST HAVE THE SAME QUALITY, BUT SINCE THEY ARE COMPRESSED AND MASTERED MORE AND MORE AND MORE AND SINCE THEY DISPLAY A SOFT COLOR OF SOUND THEY SEEM WARMER WITH LOWER HIGH FREQS.
SO COMPARED TO A CD ON THE SAME AMP EQ CONFIGURATION YOU WILL THINK THAT THE CD IS FULL OF CRISPS AND ANNOYING HIGH FREQS ESP WITH TRANCE! .
THIS COMPANY BELOW HAS A HISTORY! SOME PICS WERE SINCE THE B&W TIMES.
Ever wondered how a record is created ??
(4 PIX SCROLL DOWN)
In Holland ( Haarlem to be more precise ) there's one of the biggest companies that are still pressing the vinyl that you are playing on your turntable"s. It is called Record Industry and in the following story will explain how this process works.
Equipmentlist of Record Industry cuttingroom
1 x Neumann cutting lathe VMS 70 (laquer)
2 x Neumann cutting lathe VMS 8o (laquer)
1 x Neumann cutting lathe VMS 82 (DMM cutter: Direct Metal Mastering)
3 x Neumann console with Neumann U1160 XP equalizers and U1173 SP compressor/limiters
2 x Sony PCM-7010 Datrecorder
2 X Marantz Professional cd speler
2 x Lexicon MPX-1
1 x Pultec EQ-P A3 Equalizer
2 x Coloursound Stereo width control
2 x Klark Teknik DN-70 realtime spectrum analyzer
PC harddisk editing systeem with Wavelab, Soundforge and several plug-ins
1. Cutting Room
When an order comes in the first thing that has to be done is the cutting of a master. This is done in the cuttingroom, wich you see on the picture.
On the left there is the cutting table and on the right are the effects that has to be used to master the original tracks. All this equipment is used for anhancing and correcting the orignal so it fits best on a vinyl at the end of the process.
2. Cutting a Master
From the supplied master (CDR, DAT or any other source) a cut is made in the cutting room.
The audio is cut onto a lacquer, an acetate layer or a DMM copper layer, (DMM for classical repertoire or albums, a lacquer for 12" items), using a cutting lathe. For both the lacquer and the DMM, the cutting lathe works with a stylus (DMM a diamond stylus, lacquer with a saffier stylus) that etches a groove into the layer. A DMM copper layer gives a better respons of the high frequencies, but results in less sub frequencies when it’s pressed to vinyl. The stylus has two coils that are positioned between magnets. The audio material is led by magnets, which cause both horizontal and vertical vibrations to the stylus. The depth of the groove depends on the intensity of the audio material. Each lacquer or DMM disk is single sided so two must be cut for a regular two sided record.
When cutting the stylus is in fact 1 rotation behind on the audio, this way corrections can still be made realtime. There is an extra ‘regular’ arm so the result can be monitored during the whole proces.
3. Quality Control
Throughout the whole manufacturing process the record is subject to comprehensive Quality Control. This allready starts when an external master is supplied. This master has to be checked under a Microscope. On a monitor the result can be seen. When everything is done and before an order can be ressed, the audio must be approved. A first testing will be made and played by QC.
Paperparts (labels, sleeves, stickers etc.) are checked by QC. Finally QC check the records which are ready to ship, to make sure the customer receives the product exactly as ordered.
4. Stampers
The next stage is the plating or galvanics; the manufacture of stampers that are used to press the records.
Each side of the record, A and B side lacquers, are sprayed with silver, forming a layer of only 0,2 micron. The sprayed lacquer is put into an electro-forming bath which bonds a nickel layer onto the silver. When a substantial layer has built up, the nickel layer is separated from the lacquer and a first master is ready. This master is called the negative. The lacquer is no longer used and disposed.
5. Copying the stampers
From the negative a positive is made, using the same process as used to make
the negative. The negative is put in the electro-forming bath, a nickel layer grows" on the negative. Next the two layers are separated from each other, leaving the original negative and the new positive. Now some real handwork has to be done, the record has to be accuratly centered and all codes has to be carved in the inside. The negative is a back-up copy, which is archived.
From the positive, the stampers are produced, again in the same electro-forming
bath. The stamper is a negative, each record requires two stampers, one for the each the A and B sides. In this way we are able to develop more than one set of stampers from the same lacquer or DMM. The stampers are used on the presses to press the grooves into the vinyl. We can press approximately 1000 to 1500 records with one set of stampers.
6. Labels
The labels on the record should be very solid. During the pressing there is a huge force on the label and a lot of heat and vapor is released. This is something paper normaly is not resistant to. So the label are first hardened in an oven to that they will survive the rest of the production process.
7. Pressing
The vinyl is transported to the press in small granular or pellet form. The raw
vinyl is formed under high pressure into a small "puck" or "biscuit". The "puck" is mechanically placed between the stampers , on which are the A and B side labels. The press closes and the stampers press the vinyl "puck", under a pressure of 150 bar in 20 seconds, into a record. The record is taken out of the press mechanically, the edges are trimmed and the record mechanically inserted into an innersleeve/discosleeve, then left flat to cool down. After every 5 records a heavy metal "spacer" is placed to enhance the hardening and cooling down process.
The records are transported by an assembly-line to a robotised storage system (the collator) here they will cool down, approximately 3 hours for 125 grams records and a whole night for 180 grams records. After the cooling down period the records are ready for packaging.
8. Packaging
The packaging is done at the finishing department, where the records are mechanically sleeved and packed into boxes ready for transportation.
Allthough the most pressings can be fitted into their sleeves automaticly, special inlays and special sleeves still are handjobs. Here you see the special edition of Pink Floyd"s Dark Side of the Moon. Released 30 years ago for the first time. This record is remastered and has all the original stickers and posters. Besides rock music nowadays also a lot of clasical music is been re-released.
[img]http://[/img]
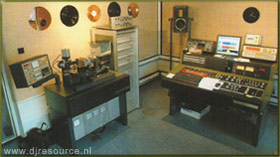
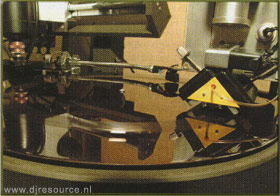
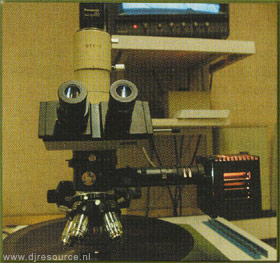
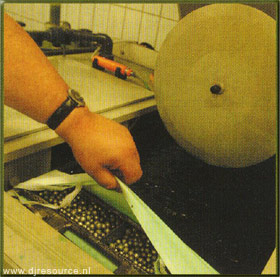
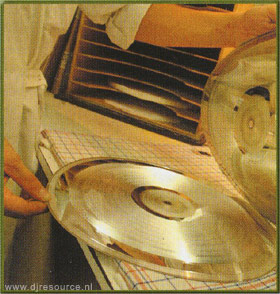
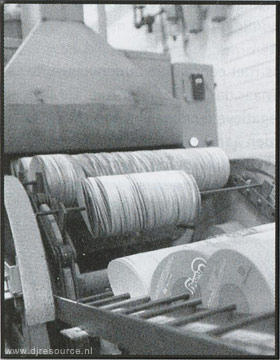
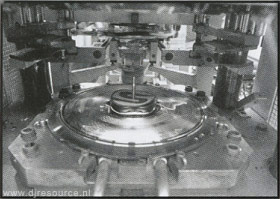
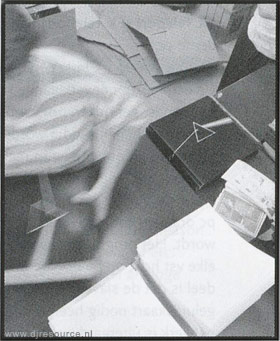
Pictures from Interface Magazine
MAKE IT STICKY!!:)